Sustainable Wastewater Solutions: The IC Process in Biosimilar Drug Manufacturing | Center Enamel
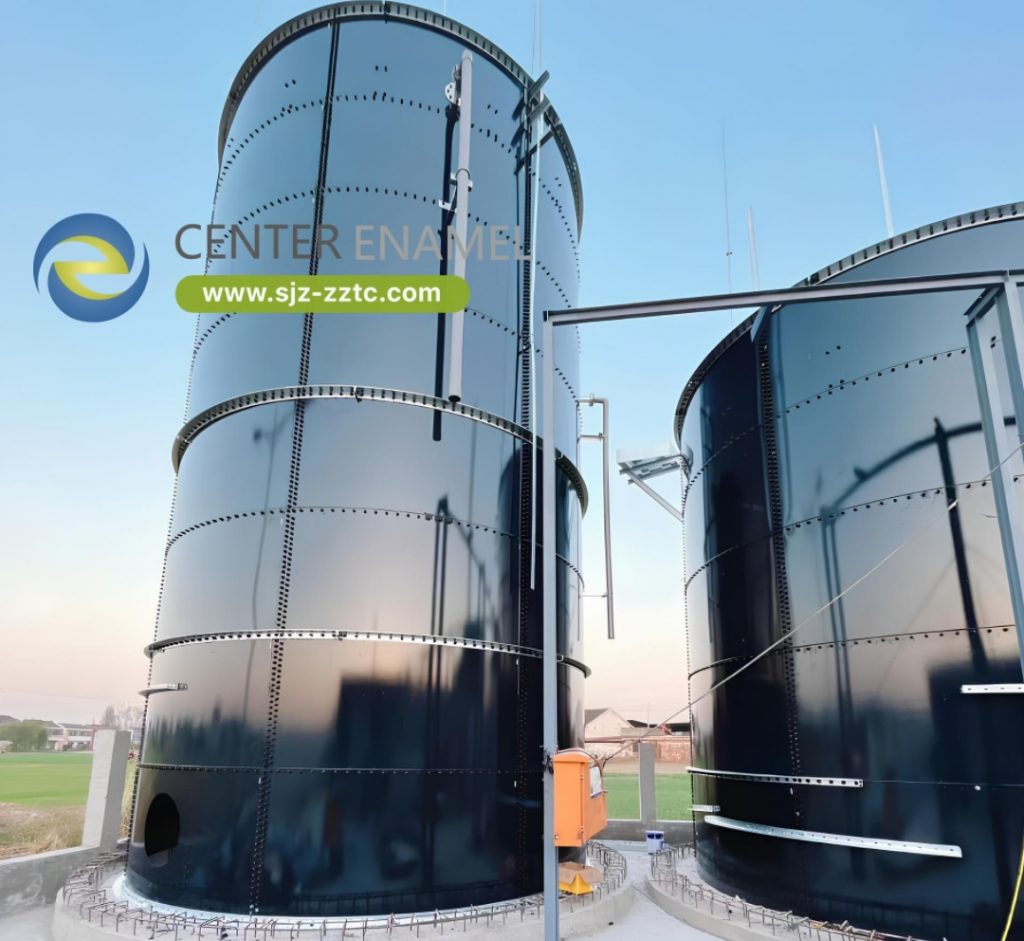
As biosimilar drug manufacturing continues to expand, the pharmaceutical industry faces increasing scrutiny regarding environmental sustainability and wastewater management. Biosimilar production involves complex processes that generate wastewater containing various organic compounds, solvents, and by-products. In response to these challenges, Center Enamel has pioneered the implementation of the Internal Circulation (IC) Process as a sustainable solution for treating wastewater in biosimilar drug manufacturing facilities.
Biosimilar drug manufacturing is characterized by stringent quality control and adherence to regulatory standards. However, the production process typically results in wastewater that contains residual biochemicals, cleaning agents, and trace amounts of active pharmaceutical ingredients. Discharging untreated or inadequately treated wastewater can lead to environmental contamination and non-compliance with national and international standards. Hence, effective wastewater treatment is critical not only for environmental protection but also for maintaining operational integrity and corporate responsibility.
Pharmaceutical wastewater presents unique challenges compared to other industrial effluents. It often requires advanced treatment technologies capable of removing both organic and inorganic contaminants while ensuring that the treated water meets strict quality criteria. This is where the IC Process has emerged as a viable and sustainable solution.
The Internal Circulation (IC) Process is an advanced wastewater treatment technology that utilizes a closed-loop system to enhance the treatment efficiency and reduce the overall environmental footprint. The IC Process is designed to optimize the removal of contaminants through enhanced mixing, controlled retention times, and efficient energy recovery. Its design supports a continuous flow operation that is both cost-effective and environmentally sustainable.
Key elements of the IC Process include:
- Enhanced Mixing and Retention: The system is engineered to ensure that wastewater is thoroughly mixed, allowing microorganisms to efficiently break down organic compounds. The enhanced retention time improves degradation rates, leading to higher removal efficiencies.
- Energy Recovery: By capturing and utilizing the biogas generated during the treatment process, the IC Process contributes to energy savings. This energy recovery aspect aligns with sustainable manufacturing practices, reducing the reliance on external energy sources.
- Compact Footprint: The IC Process is designed to occupy less physical space compared to traditional wastewater treatment systems. This compact design is particularly beneficial in pharmaceutical manufacturing facilities where space is at a premium.
- Automated Control Systems: Advanced monitoring and automation ensure that the process remains within optimal operational parameters. Real-time adjustments help maintain high efficiency even when wastewater characteristics vary.
Benefits of the IC Process in Biosimilar Drug Manufacturing
Implementing the IC Process within biosimilar drug manufacturing offers several significant advantages:
- Compliance with Regulatory Standards:
The IC Process is designed to achieve the rigorous wastewater discharge standards required by regulatory bodies. By effectively removing contaminants, the system ensures that treated water is safe for discharge or potential reuse in non-critical applications. - Operational Efficiency:
The continuous, closed-loop nature of the IC Process minimizes downtime and reduces the need for manual intervention. This leads to consistent performance and lower operational costs over the long term. - Reduced Environmental Impact:
By enhancing contaminant removal and enabling energy recovery, the IC Process significantly reduces the overall environmental footprint of biosimilar drug manufacturing operations. This aligns with global trends towards greener industrial practices and sustainability. - Cost-Effectiveness:
The compact design and energy-efficient operation of the IC Process result in lower capital and operational expenditures. In addition, the reduction in chemical usage and maintenance requirements contributes to long-term savings. - Scalability and Flexibility:
The modular design of the IC Process allows for easy scalability, making it suitable for both small-scale operations and large pharmaceutical manufacturing plants. The system can be customized to accommodate varying volumes and contaminant loads, ensuring optimal performance across different production scenarios. - Enhanced Process Stability:
The automation and real-time monitoring inherent in the IC Process provide a high degree of process control. This stability is essential in biosimilar production, where fluctuations in wastewater characteristics could compromise product quality and safety.
Center Enamel’s Commitment to Sustainable Solutions
Center Enamel has a longstanding reputation for delivering high-quality, sustainable solutions across various industries. Our expertise in advanced wastewater treatment technologies, including the IC Process, has positioned us as a trusted partner in the pharmaceutical sector. By integrating the IC Process into biosimilar drug manufacturing, we enable our clients to not only meet regulatory requirements but also enhance operational efficiency and environmental stewardship.
Our approach is grounded in precision engineering and continuous innovation. We work closely with our clients to design, customize, and implement wastewater treatment systems that are tailored to the specific needs of their manufacturing processes. This commitment to quality ensures that every solution we deliver not only meets but exceeds industry standards.
For organizations seeking to adopt sustainable wastewater solutions in their biosimilar drug manufacturing operations, Center Enamel provides a proven, state-of-the-art IC Process that delivers both performance and long-term value.
Contact Center Enamel today to learn more about how our sustainable wastewater solutions can transform your manufacturing processes and support your commitment to environmental responsibility.