Internal Circulation Reactors for Sustainable Wastewater Management in Drug Production | Center Enamel
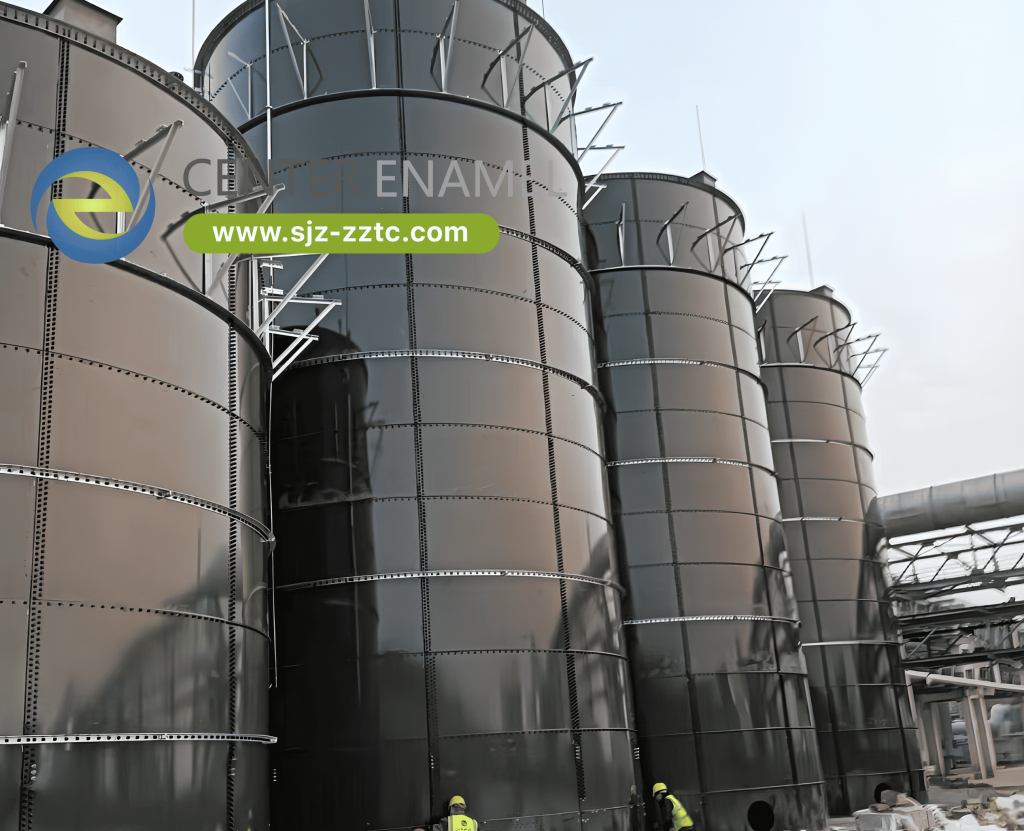
In the pharmaceutical manufacturing sector, stringent regulatory standards and the need for environmental stewardship necessitate efficient wastewater management solutions. Internal circulation (IC) reactors have emerged as an advanced technology capable of treating complex pharmaceutical effluents while ensuring process stability and operational efficiency. Center Enamel delivers high-performance IC reactors that are engineered to meet the demanding requirements of drug production facilities, ensuring sustainable wastewater treatment and long-term reliability.
Internal circulation reactors are designed to optimize the anaerobic digestion process by promoting enhanced mixing and improved contact between wastewater and microbial communities. Unlike conventional reactors, IC reactors incorporate an internal recirculation system that ensures uniform distribution of substrates, thereby enhancing the degradation of organic compounds. In pharmaceutical wastewater treatment, this results in efficient removal of contaminants while minimizing the formation of undesirable by-products.
Pharmaceutical production generates wastewater that often contains a complex mixture of organic compounds, solvents, and trace contaminants. Effective treatment of these effluents is critical not only for regulatory compliance but also for protecting public health and minimizing environmental impact. IC reactors provide a controlled environment where microbial processes can be carefully managed, ensuring the degradation of harmful substances and reducing chemical oxygen demand (COD) levels. This level of treatment is essential in drug production, where even trace pollutants can compromise both product quality and environmental safety.
Technical Advantages of IC Reactors in Pharmaceutical Applications
Enhanced Process Efficiency:
The design of IC reactors ensures continuous mixing and optimal retention times, which are essential for maintaining a stable microbial ecosystem. This promotes the effective breakdown of complex organic compounds typically found in pharmaceutical wastewater. The internal circulation mechanism minimizes dead zones within the reactor, ensuring that all influent receives adequate treatment and that biogas production remains consistent.
Robust Contaminant Removal:
Pharmaceutical effluents often contain recalcitrant compounds that require advanced treatment methods. IC reactors are capable of handling high-strength wastewater through a controlled anaerobic process. The combination of thorough mixing and extended contact time between the wastewater and microorganisms results in high removal rates of organic pollutants, nutrients, and other contaminants.
Energy Recovery and Operational Cost Savings:
One of the notable benefits of IC reactors is their ability to generate biogas as a by-product of the anaerobic digestion process. Although the primary objective in pharmaceutical wastewater treatment is contaminant removal, the captured biogas can be utilized to offset energy costs or even contribute to on-site power generation. This integrated approach not only enhances overall process sustainability but also provides economic advantages by reducing operational expenditures.
Compact and Modular Design:
Space is often at a premium in industrial settings, including pharmaceutical production facilities. IC reactors are designed to be compact and modular, allowing for flexible installation that can be adapted to the specific layout and capacity requirements of a plant. The scalability of these reactors ensures that both small-scale operations and large manufacturing sites can benefit from their advanced treatment capabilities.
Real-Time Process Monitoring:
Modern IC reactor systems incorporate advanced sensors and control mechanisms that facilitate real-time monitoring of critical process parameters. By continuously assessing factors such as temperature, pH, and biogas production, operators can ensure that the treatment process remains within optimal ranges. This proactive approach to process management not only enhances treatment efficiency but also minimizes the risk of operational disruptions.
Sustainability and Compliance Benefits
Sustainable wastewater management is integral to reducing the environmental footprint of drug production. IC reactors contribute to sustainability in several ways:
- Reduced Greenhouse Gas Emissions:
By efficiently capturing and converting organic waste into biogas, IC reactors help lower the emission of greenhouse gases, such as methane. This contributes to a reduction in the overall carbon footprint of the production facility. - Minimized Chemical Usage:
The biological treatment process facilitated by IC reactors lessens the need for chemical additives that are typically used in conventional treatment methods. This reduction in chemical usage minimizes the potential for secondary pollution and aligns with the principles of green chemistry. - Compliance with Regulatory Standards:
Pharmaceutical manufacturers are subject to rigorous environmental regulations. The high removal efficiencies achieved by IC reactors ensure that treated effluent consistently meets or exceeds discharge standards. This compliance not only protects the environment but also safeguards the reputation and operational continuity of the production facility.
Why Choose Center Enamel for IC Reactor Solutions?
Center Enamel has over three decades of experience in designing and manufacturing advanced storage and reactor systems for industrial applications. Our IC reactors are developed with a focus on precision engineering and sustainability. Key factors that set our solutions apart include:
- Innovative Design and Engineering:
Our reactors are engineered using state-of-the-art computational modeling and robust design principles, ensuring optimal performance under demanding conditions. - Customization for Specific Applications:
We understand that each pharmaceutical production facility has unique wastewater characteristics. Center Enamel offers tailored reactor configurations and process control options to meet the specific needs of your operation. - Global Expertise and Quality Assurance:
With a proven track record of successful installations worldwide, Center Enamel adheres to stringent international quality standards. Our products are designed to deliver reliable, long-term performance while ensuring operational safety and environmental compliance. - Commitment to Sustainability:
Our approach integrates sustainable practices throughout the design, manufacturing, and operational phases. By choosing Center Enamel, you are investing in technology that not only improves process efficiency but also supports broader environmental objectives.
Center Enamel’s internal circulation reactors provide a robust solution for treating complex pharmaceutical effluents, offering superior contaminant removal, energy recovery, and process reliability. Our advanced reactor systems are engineered to deliver consistent performance while meeting the demanding regulatory and operational requirements of drug production facilities.
By integrating our state-of-the-art IC reactor solutions into your wastewater treatment process, you can achieve both enhanced environmental compliance and long-term operational savings. For more information on how Center Enamel can support sustainable wastewater management in your drug production facility, please contact us today.