Eco-Friendly IC Bioreactor for Zero-Liquid Discharge in Pharmaceutical Factories
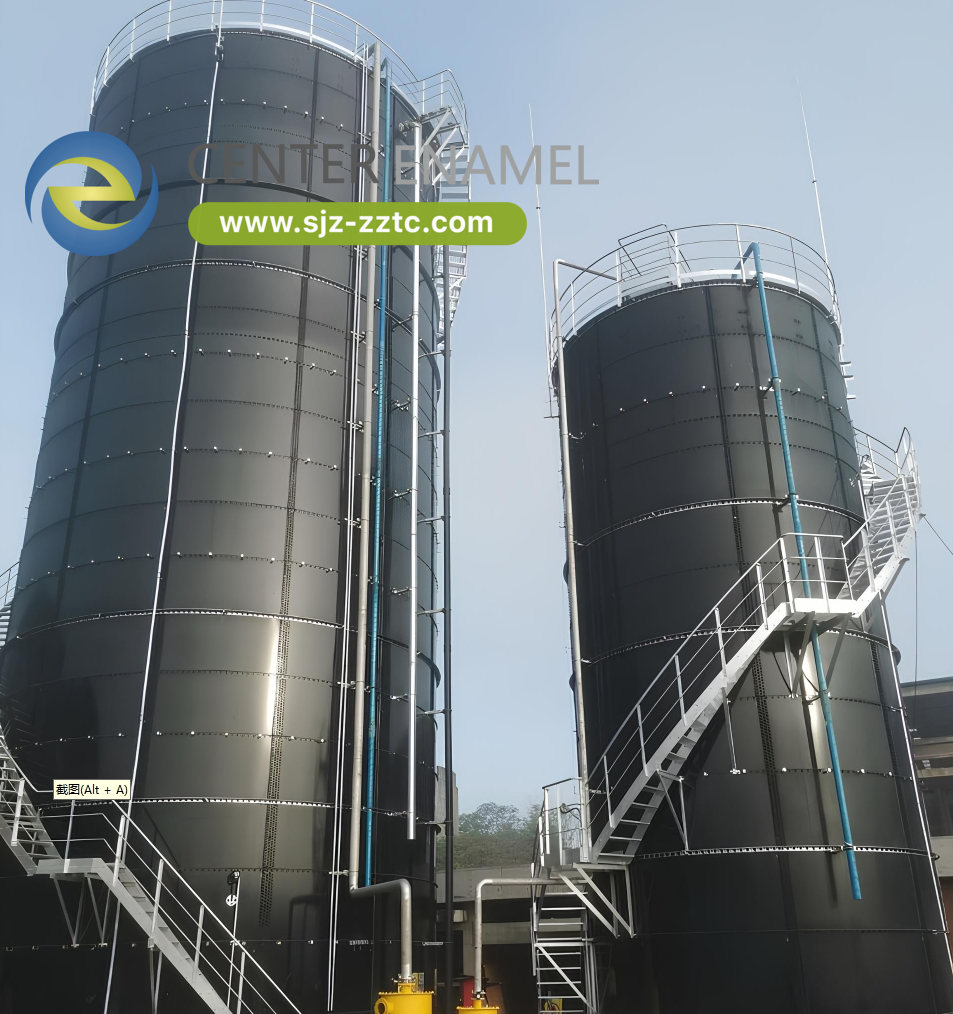
Pharmaceutical manufacturing is subject to stringent environmental regulations and quality control standards, making the treatment of process wastewater both a critical and complex task. In response, innovative solutions such as the eco-friendly Internal Circulation (IC) bioreactor have emerged to meet these challenges. Center Enamel is at the forefront of this technology, offering an IC bioreactor specifically engineered to facilitate zero-liquid discharge (ZLD) in pharmaceutical factories.
Zero-liquid discharge is an advanced wastewater management strategy that aims to recycle and recover all process water, leaving no effluent to discharge into the environment. For pharmaceutical facilities, where effluents may contain residual solvents, active pharmaceutical ingredients, and other contaminants, achieving ZLD is not only a regulatory requirement but also a vital component of sustainable operation. By eliminating wastewater discharge, companies can minimize environmental risks, reduce water consumption, and lower the cost associated with effluent treatment and disposal.
The IC bioreactor operates on the principle of enhanced microbial degradation through internal circulation. This design ensures thorough mixing and optimized contact between microorganisms and wastewater contaminants, thereby accelerating the biodegradation process. The reactor’s architecture is specifically tailored to handle the complex composition of pharmaceutical effluent, which often includes a mixture of organic compounds, chemicals, and trace pharmaceuticals.
Key operational attributes of the IC bioreactor include:
- Optimized Internal Circulation: The reactor’s design facilitates continuous mixing, ensuring that microbial activity is evenly distributed throughout the treatment volume. This results in consistent and efficient breakdown of contaminants.
- Enhanced Microbial Activity: By maintaining ideal conditions for microbial growth and metabolism, the IC bioreactor maximizes the conversion of harmful organic compounds into benign end-products.
- Process Stability: Integrated process controls monitor critical parameters such as pH, temperature, and oxygen levels, ensuring that the reactor operates within the optimal range for microbial efficiency.
Eco-Friendly Design and Sustainability
Sustainability is at the core of Center Enamel’s design philosophy. The eco-friendly IC bioreactor is constructed using durable, corrosion-resistant materials that not only withstand the chemically aggressive nature of pharmaceutical wastewater but also minimize maintenance requirements over its operational life. Its energy-efficient design reduces overall power consumption, contributing to both operational cost savings and a lower carbon footprint.
In addition, the reactor’s modular design allows for scalability and customization, ensuring that it can be adapted to the specific wastewater treatment needs of different pharmaceutical facilities. By integrating the IC bioreactor with subsequent treatment processes—such as advanced filtration, evaporation, and crystallization—pharmaceutical plants can achieve true zero-liquid discharge, recovering nearly all process water for reuse.
Integration into Pharmaceutical Manufacturing
The application of an eco-friendly IC bioreactor within a pharmaceutical plant begins with a detailed assessment of the facility’s wastewater characteristics. This assessment informs the customization of the reactor’s design, ensuring that it can effectively treat the unique blend of contaminants present in the effluent.
Once installed, the IC bioreactor operates as the first critical step in a comprehensive wastewater treatment train. Here, the biologically mediated degradation of organic pollutants is optimized, reducing the load on downstream processes. The treated effluent is then subjected to additional purification steps, including:
- Advanced Filtration: To remove any remaining suspended solids and fine particulates.
- Evaporation and Crystallization: To recover water and transform residual salts and other contaminants into solid waste, which can be managed safely.
- Polishing Processes: To ensure that the final reclaimed water meets the high purity standards required for reuse in pharmaceutical manufacturing.
The seamless integration of these processes enables pharmaceutical facilities to achieve ZLD, ensuring that every drop of water is reused within the plant while hazardous waste is minimized.
Economic and Environmental Benefits
Implementing an eco-friendly IC bioreactor for ZLD in pharmaceutical factories delivers a range of significant benefits:
- Regulatory Compliance: By achieving ZLD, facilities can meet or exceed local and international environmental regulations, thereby avoiding potential fines and sanctions.
- Cost Savings: The recovery and reuse of process water reduce the need for fresh water intake and lower wastewater treatment costs. Moreover, minimizing effluent discharge translates into lower disposal expenses.
- Enhanced Sustainability: Zero-liquid discharge contributes to a reduced environmental footprint by minimizing water consumption and preventing the release of contaminants into surrounding ecosystems.
- Operational Reliability: The durable, low-maintenance design of the IC bioreactor ensures consistent performance over the long term, reducing downtime and maintenance-related disruptions.
Why Choose Center Enamel?
With over 30 years of experience in designing and manufacturing advanced storage and treatment solutions, Center Enamel is uniquely positioned to provide high-performance IC bioreactors tailored for the pharmaceutical industry. Our systems are engineered to meet the rigorous demands of modern manufacturing, delivering both reliability and sustainability. We work closely with our clients to customize each system according to specific operational requirements, ensuring optimal integration and maximum efficiency.
Center Enamel’s commitment to innovation and quality means that our IC bioreactors not only meet stringent environmental regulations but also deliver tangible economic benefits through water reuse and waste minimization. For pharmaceutical manufacturers committed to sustainability and operational excellence, Center Enamel’s eco-friendly IC bioreactor offers a proven pathway to achieving zero-liquid discharge and a greener future. Contact us today to explore how our advanced wastewater treatment solutions can be tailored to your facility’s specific needs.