CSTR Reactor for Treating High-Protein Wastewater from Meat Processing: Center Enamel’s Innovative Approach
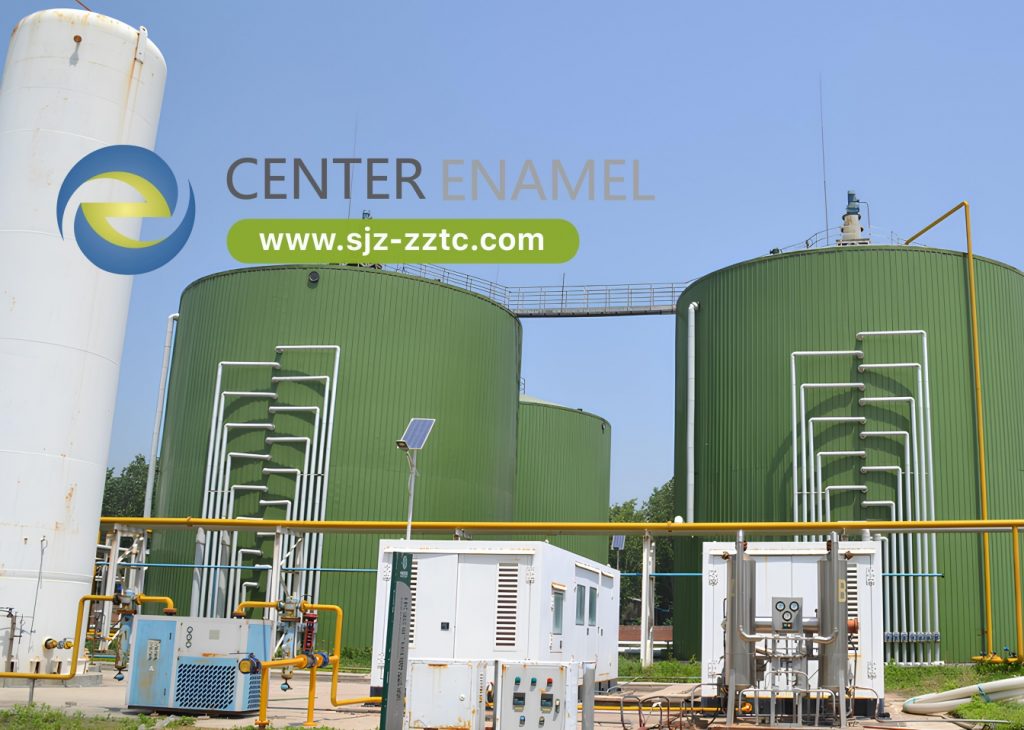
The meat processing industry generates significant volumes of high-protein wastewater that pose complex treatment challenges. Rich in organic matter, proteins, fats, and suspended solids, this wastewater demands robust and efficient treatment solutions to meet increasingly stringent environmental regulations. Center Enamel addresses this challenge with its advanced Continuous Stirred Tank Reactor (CSTR) technology—an engineered solution designed to optimize the biodegradation of high-protein effluents while ensuring operational stability and cost-effectiveness.
A Continuous Stirred Tank Reactor (CSTR) is a well-established biochemical treatment system widely used in industrial wastewater applications. In the context of meat processing, the CSTR reactor is tailored to handle wastewater with high organic loads by providing a controlled, homogenous environment in which biological processes can occur efficiently. The continuous mixing inherent to the CSTR design ensures that microbial populations are evenly distributed, which enhances the degradation of proteins and other complex organic compounds.
Key Challenges in Treating Meat Processing Wastewater
Meat processing effluents present several unique challenges:
- High Organic and Nitrogen Content: Elevated concentrations of proteins and other organic matter lead to high Chemical Oxygen Demand (COD) and Biochemical Oxygen Demand (BOD), requiring effective treatment to prevent environmental harm.
- Fat and Oil Accumulation: Fats and oils can create obstacles in conventional treatment processes, potentially leading to the formation of scum layers and interference with microbial activity.
- Variable Flow Rates and Loads: The production process often results in fluctuating wastewater flows and pollutant concentrations, necessitating a treatment system that can adapt to these variations without compromising performance.
- Foaming and Odor Issues: The biodegradation of proteins and fats can produce foaming and unpleasant odors, both of which need to be managed to maintain safe and compliant operational conditions.
How Center Enamel’s CSTR Reactor Addresses These Challenges
1. Enhanced Mixing and Homogeneity The design of Center Enamel’s CSTR reactor ensures continuous and thorough mixing of the wastewater. This uniform distribution of contaminants and microbial populations facilitates efficient degradation of high-protein compounds, preventing localized high concentrations that could impair treatment performance. Consistent mixing also minimizes the risk of dead zones where pollutants might accumulate, thereby optimizing the overall treatment process.
2. Optimized Biological Process By maintaining a stable and controlled environment, the CSTR reactor enhances the performance of anaerobic and aerobic microbial processes. This is critical for breaking down complex proteins and fats into simpler compounds that can be more readily assimilated by the microbial community. The controlled conditions help maintain the optimal pH, temperature, and dissolved oxygen levels, ensuring maximum biodegradation efficiency and effective nutrient removal.
3. Adaptability to Variable Loads The inherent flexibility of the CSTR design allows it to accommodate fluctuations in wastewater flow and pollutant load—common characteristics of meat processing effluent. The reactor’s continuous operation ensures that sudden increases in organic load do not overwhelm the system, thereby preserving treatment efficiency and system stability.
4. Integration of Advanced Monitoring and Control Systems Center Enamel’s CSTR reactors incorporate state-of-the-art sensors and control technologies that monitor critical parameters such as pH, temperature, and dissolved oxygen in real-time. These automated systems enable rapid adjustments to process conditions, ensuring that the reactor operates within optimal ranges at all times. This proactive management not only enhances treatment performance but also minimizes the risk of operational failures.
5. Robust Construction for Industrial Environments Constructed from high-grade, corrosion-resistant materials, the CSTR reactor is built to withstand the rigorous conditions typical of meat processing facilities. The reactor’s design minimizes maintenance requirements and extends the service life of the unit, ensuring reliable performance over prolonged operational periods.
Benefits for the Meat Processing Industry
Environmental Compliance and Sustainability By effectively reducing the organic load, nitrogen, and other pollutants in wastewater, the CSTR reactor helps meat processing plants meet strict discharge regulations. This not only protects local water resources but also supports the industry’s broader commitment to environmental stewardship.
Operational Efficiency and Cost Savings The robust design and automation integrated into the CSTR reactor result in lower operational and maintenance costs. The system’s ability to handle variable loads without compromising performance translates into reduced downtime and enhanced overall efficiency. Moreover, improved treatment efficiency can lead to potential cost savings through energy recovery and reduced sludge handling expenses.
Improved Water Quality for Reuse Efficient treatment of high-protein wastewater not only facilitates compliance with environmental standards but also produces high-quality effluent that may be suitable for water reuse applications. This contributes to sustainable water management practices—a critical consideration in water-scarce regions or facilities looking to optimize resource utilization.
Why Choose Center Enamel?
Proven Expertise and Engineering Excellence With decades of experience in industrial storage and treatment solutions, Center Enamel is a trusted leader in designing and manufacturing advanced CSTR reactors. Our systems are the result of rigorous research, innovative engineering, and a commitment to delivering high-performance solutions that meet the demanding needs of modern industrial applications.
Customizable Solutions for Specific Needs We recognize that every meat processing facility has unique wastewater characteristics and operational challenges. Center Enamel offers customizable reactor designs tailored to the specific needs of each client, ensuring that our CSTR reactors integrate seamlessly with existing processes and infrastructure.
Global Reach and Quality Assurance Center Enamel’s products are deployed in industrial facilities across more than 100 countries, a testament to our global reputation for reliability and excellence. Our manufacturing processes adhere to the highest international quality standards, ensuring that every reactor delivered performs consistently under the most challenging conditions.
Commitment to Sustainability and Innovation Our focus on sustainable engineering practices drives continuous improvements in our reactor designs. By integrating energy-efficient technologies and eco-friendly materials, Center Enamel not only enhances wastewater treatment performance but also contributes to the overall sustainability goals of our clients.
The treatment of high-protein wastewater from meat processing plants presents a unique set of challenges that demand innovative and robust solutions. Center Enamel’s CSTR reactor offers a highly effective approach, combining advanced mixing, optimized biological processes, and state-of-the-art monitoring systems to deliver superior wastewater treatment performance. By ensuring regulatory compliance, reducing operational costs, and enhancing water reuse potential, our CSTR reactor stands as a critical asset for the meat processing industry.
For organizations seeking a reliable, efficient, and sustainable solution to manage high-protein wastewater, Center Enamel is the partner of choice. Contact us today to learn more about how our cutting-edge CSTR reactors can transform your wastewater treatment process and support your environmental and operational objectives.