Continuous Stirred Tank Reactor Advantages - Center Enamel
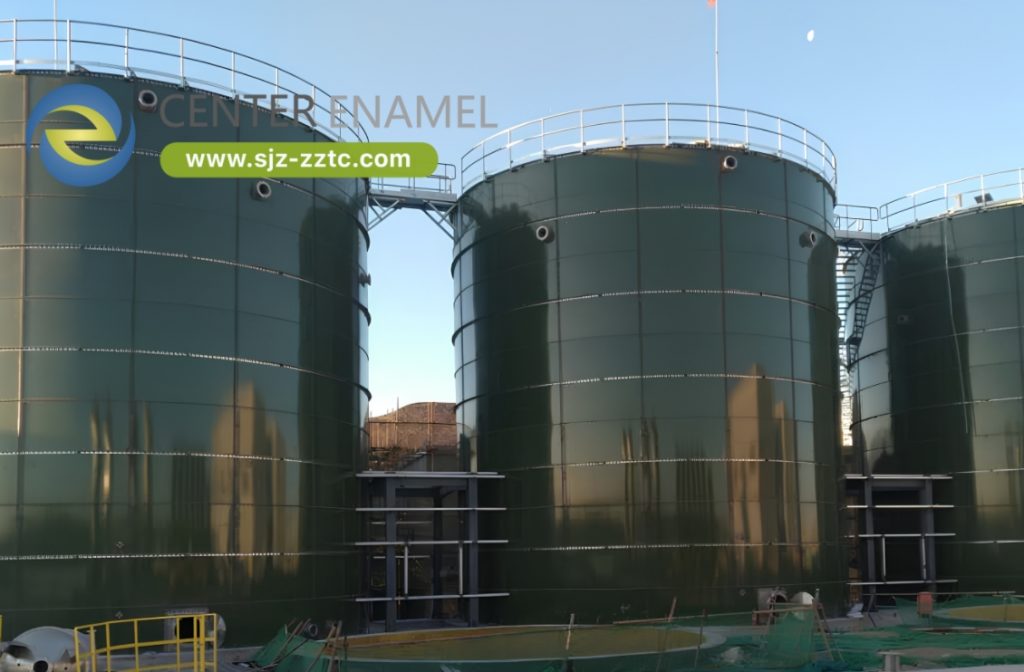
In today’s competitive industrial landscape, efficiency and precision are paramount. Continuous Stirred Tank Reactors (CSTRs) have emerged as a cornerstone technology for a variety of chemical, pharmaceutical, and food processing applications. At Center Enamel, we leverage decades of expertise to design and manufacture advanced CSTR systems that deliver optimal performance, process consistency, and scalability. This article explores the fundamental advantages of continuous stirred tank reactors and how our solutions can elevate your process operations.
A Continuous Stirred Tank Reactor is a type of reactor in which reactants are continuously fed into the vessel and mixed thoroughly, ensuring a homogeneous reaction environment. Unlike batch reactors, where reactions occur in discrete cycles, CSTRs allow for uninterrupted processing. This continuous operation enables steady-state conditions, improved product quality, and consistent output—all critical factors in large-scale production and research applications.
Key Advantages of Continuous Stirred Tank Reactors
1. Uniform Mixing and Enhanced Product Consistency
One of the most significant benefits of a CSTR is its ability to maintain a homogenous mixture throughout the reactor. The continuous agitation and stirring facilitate uniform temperature, concentration, and reaction rates across the entire reactor volume. This uniformity minimizes the formation of by-products, ensures consistent product quality, and supports tighter process control.
- Homogeneity: Ensures that reactants are evenly distributed, reducing localized concentration gradients.
- Temperature Control: Consistent agitation helps in dissipating heat, minimizing the risk of hot spots that can lead to side reactions.
- Product Quality: The uniform reaction environment results in consistent product specifications, which is critical in industries with strict quality standards.
2. Continuous Operation and Improved Throughput
CSTRs are designed for continuous processing, allowing for a steady stream of production without the downtime associated with batch operations. This continuous flow not only improves overall production throughput but also simplifies process scheduling and inventory management.
- Steady-State Processing: Enables stable and predictable operating conditions, leading to better control over reaction kinetics.
- Increased Productivity: Continuous feed and withdrawal of materials reduce idle time, ensuring that production is maintained around the clock.
- Scalability: Continuous processes can be scaled up more efficiently than batch processes, offering flexibility as production demands increase.
3. Superior Heat Transfer Capabilities
Efficient heat management is critical in maintaining optimal reaction conditions and ensuring safety, especially in exothermic reactions. The design of CSTRs typically includes advanced agitation and cooling systems that promote excellent heat transfer.
- Rapid Heat Dissipation: Continuous stirring enhances heat transfer from the reaction mixture to the reactor walls or cooling jackets.
- Temperature Uniformity: Maintaining a consistent reaction temperature helps prevent thermal runaway and ensures reaction efficiency.
- Enhanced Safety: Superior heat control minimizes the risk of overheating and potential reactor damage, crucial for high-stakes industrial processes.
4. Operational Flexibility and Adaptability
The design of continuous stirred tank reactors lends itself to a high degree of operational flexibility. CSTRs can handle a wide range of reaction types—from simple mixing processes to complex catalytic reactions—making them versatile tools in both research and industrial settings.
- Versatile Reaction Handling: Capable of processing reactions involving solids, liquids, and gases.
- Adaptability: Suitable for both homogeneous and heterogeneous reactions, with easy integration of catalysts and other additives.
- Process Optimization: Advanced control systems allow for real-time adjustments to mixing speeds, temperature, and flow rates, ensuring optimal reaction conditions are maintained.
5. Reduced Fouling and Maintenance Requirements
Fouling—the accumulation of unwanted materials on reactor surfaces—can impede reactor efficiency and increase maintenance costs. The continuous mixing inherent in CSTRs helps to minimize fouling, thereby extending the reactor's operational life and reducing downtime.
- Self-Cleaning Action: The vigorous stirring action prevents the deposition of solids and other contaminants on the reactor walls.
- Lower Maintenance Costs: Reduced fouling means fewer cleaning cycles and less frequent maintenance shutdowns.
- Enhanced Reliability: Consistent operation with minimal interruptions improves overall system reliability and reduces lifecycle costs.
Applications of Continuous Stirred Tank Reactors
Continuous Stirred Tank Reactors are deployed across a myriad of industries, underscoring their versatility and efficiency:
- Chemical Processing: Widely used for reactions that require precise temperature and concentration control, such as polymerization, esterification, and oxidation processes.
- Pharmaceutical Manufacturing: Ensure high-quality synthesis of active pharmaceutical ingredients (APIs) with stringent purity and consistency requirements.
- Food and Beverage Production: Facilitate the continuous processing of ingredients and products, ensuring consistent flavor profiles and quality.
- Environmental and Waste Treatment: Employed in bioreactors and other waste treatment applications where controlled reaction environments are essential for breaking down pollutants.
Why Choose Center Enamel’s CSTR Solutions?
At Center Enamel, we understand that the demands of modern industrial processes require reactor systems that are both robust and adaptable. Our continuous stirred tank reactors are designed to meet these needs with advanced engineering and high-quality manufacturing standards.
- Precision Engineering: Our CSTRs are developed using state-of-the-art design principles and are fabricated with precision to ensure optimal performance.
- Customizable Systems: We offer tailored solutions that cater to the specific requirements of your process, from reactor size and configuration to advanced control systems.
- Global Expertise: With a legacy spanning over three decades, Center Enamel has successfully implemented continuous reactor solutions for clients in more than 100 countries.
- Sustainable Operations: Our reactors are designed to maximize efficiency and reduce energy consumption, supporting both economic and environmental sustainability.
Center Enamel’s commitment to innovation and quality ensures that our CSTR solutions not only meet but exceed industry standards, delivering reliable and scalable performance for your process operations.
For professionals seeking to optimize their production capabilities and achieve superior operational efficiency, Center Enamel’s continuous stirred tank reactors offer a sophisticated and proven solution. Contact us today to learn more about how our advanced reactor systems can transform your process operations and drive sustainable growth.