Center Enamel – IC Process Stage Optimization for Maximum Biogas Yield
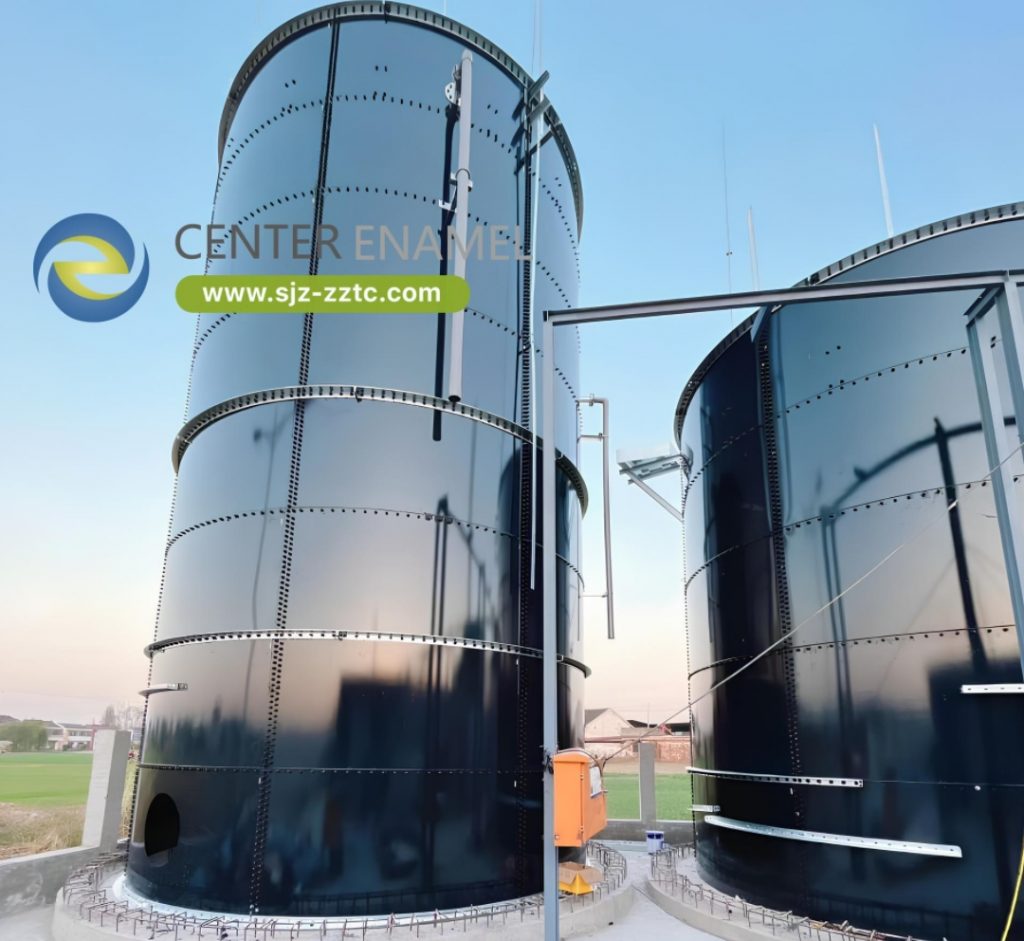
In today’s energy landscape, optimizing renewable fuel production is not just an operational advantage—it’s an environmental imperative. The Internal Circulation (IC) process stage in anaerobic digestion plays a critical role in transforming organic waste into biogas. By fine-tuning this phase, energy operators can significantly increase biogas yield and enhance overall system efficiency. At Center Enamel, we apply advanced engineering principles and state-of-the-art technology to optimize the IC process stage for maximum biogas production.
The IC process stage is a vital segment of the anaerobic digestion system where the breakdown of organic substrates occurs most efficiently. In this phase, a controlled circulation mechanism ensures that the feedstock is uniformly distributed, enhancing contact with microbial communities responsible for biogas generation. This internal recirculation not only accelerates the hydrolysis and acidogenesis processes but also stabilizes the reactor’s operating conditions.
Key factors influencing the IC stage include:
- Retention Time: Adequate exposure of organic matter to active microbes is essential for complete digestion.
- Mixing Intensity: Uniform mixing prevents the formation of dead zones, ensuring consistent microbial activity.
- Temperature and pH Control: Maintaining optimal environmental conditions is crucial for microbial metabolism and process stability.
Strategies for Process Optimization
Optimizing the IC process stage involves a multifaceted approach that integrates real-time monitoring, precise control systems, and adaptive engineering solutions. Center Enamel’s methodology for process stage optimization is rooted in rigorous data analytics and robust system design. Here are some of the key strategies we implement:
- Advanced Sensor Integration Utilizing a network of high-precision sensors, our systems continuously monitor critical parameters such as temperature, pH, oxidation-reduction potential (ORP), and volatile fatty acids. Real-time data collection enables immediate corrective actions, ensuring that the reactor environment remains within the optimal range for biogas production.
- Dynamic Process Control Automated control systems adjust the mixing intensity and internal recirculation flow rates in response to real-time sensor data. This dynamic control helps maintain ideal conditions for microbial activity, thereby enhancing the conversion efficiency of organic substrates into biogas.
- Optimized Retention Time Through meticulous calibration of hydraulic retention time (HRT), we ensure that the substrates remain in the reactor long enough to undergo complete degradation, yet are processed efficiently to avoid unnecessary delays. This balance maximizes the overall biogas yield while minimizing reactor downtime.
- Enhanced Mixing Techniques Our design improvements incorporate advanced mixing technologies that promote uniform distribution of substrates and microbial populations. Enhanced mixing reduces the risk of stratification and the development of inhibitory conditions, leading to a more stable and productive digestion process.
- Microbial Community Management A well-balanced microbial ecosystem is fundamental to efficient anaerobic digestion. By optimizing nutrient supply and maintaining consistent operating conditions, our process ensures that both hydrolytic and methanogenic bacteria thrive, resulting in improved biogas composition and yield.
Innovative Solutions from Center Enamel
Center Enamel leverages over three decades of expertise in storage and process engineering to deliver tailored solutions that push the boundaries of biogas production. Our approach to IC process stage optimization is both holistic and scientifically rigorous. Key innovations include:
- Real-Time Data Analytics: Our proprietary analytics platforms interpret sensor data to predict performance trends, allowing for proactive adjustments that optimize biogas yield. This predictive capability is essential for minimizing fluctuations in reactor performance.
- Modular Reactor Design: Our systems are designed with modularity in mind, enabling seamless scalability and easy retrofitting into existing infrastructure. This flexibility means that facilities can upgrade their processes without extensive overhauls, ensuring a smooth transition to optimized operations.
- Energy Efficiency and Sustainability: Optimizing the IC stage not only boosts biogas production but also contributes to a reduction in energy consumption across the facility. By maintaining a stable and efficient process, operators can achieve higher methane yields while reducing greenhouse gas emissions—a win-win for both operational costs and environmental sustainability.
- Continuous R&D Investment: At Center Enamel, we are committed to ongoing research and development. Our dedicated teams work to integrate the latest advances in sensor technology, process control, and microbial management, ensuring that our solutions remain at the forefront of anaerobic digestion technology.
Benefits of IC Process Stage Optimization
Implementing optimized IC process strategies yields multiple advantages for energy plants and biogas facilities:
- Increased Biogas Yield: By maintaining optimal reactor conditions, the conversion efficiency of organic substrates is maximized, resulting in higher biogas production and improved methane content.
- Enhanced Process Stability: Continuous monitoring and adaptive control reduce the variability in reactor performance, ensuring a steady and reliable biogas supply.
- Reduced Operational Costs: Greater process efficiency translates to lower energy consumption and reduced maintenance requirements, delivering significant cost savings over the lifecycle of the system.
- Environmental Benefits: Maximizing biogas yield improves the overall sustainability of waste-to-energy operations, contributing to a reduction in greenhouse gas emissions and supporting environmental compliance initiatives.
Optimizing the IC process stage is essential for unlocking the full potential of biogas production. At Center Enamel, our integrated approach—combining advanced sensor technology, dynamic control systems, and precision engineering—ensures that every biogas facility can achieve maximum efficiency and output. Our commitment to innovation and sustainability drives us to continuously improve our solutions, empowering energy operators to meet the growing demand for renewable energy.
For industry professionals seeking to enhance their biogas yield through state-of-the-art process optimization, Center Enamel offers unparalleled expertise and tailored solutions. Contact us today to learn more about how our optimized IC process stage technology can elevate your biogas production capabilities and contribute to a cleaner, more sustainable energy future.