Automated IC Process Management for Streamlined Anaerobic Digestion Operations
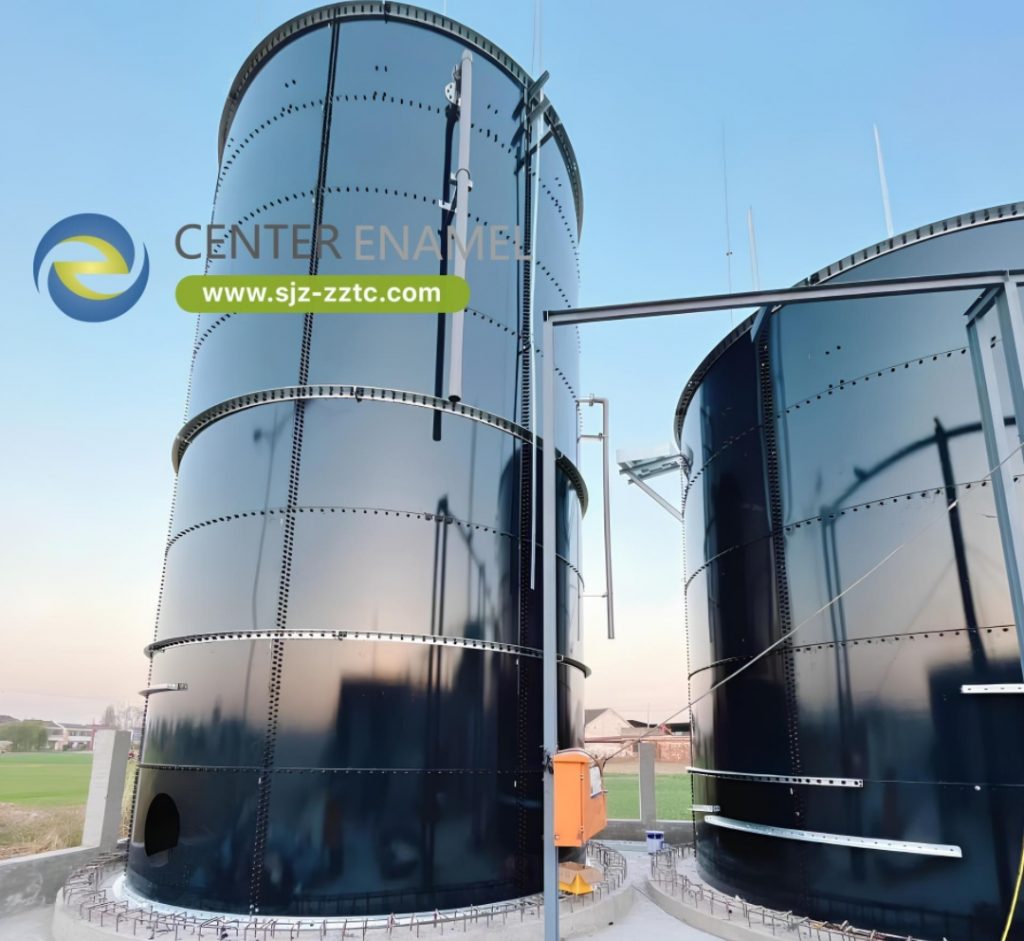
Anaerobic digestion (AD) is a key technology in renewable energy and waste management, efficiently converting organic waste into biogas and valuable byproducts. Among the various AD reactor designs, Internal Circulation (IC) reactors stand out for their high efficiency and compact footprint. However, optimizing IC reactors for maximum performance requires precise process control. Automated IC process management is revolutionizing anaerobic digestion operations by enhancing efficiency, stability, and sustainability.
IC reactors are advanced high-rate anaerobic digesters designed to treat wastewater with high organic loads. They operate by maintaining a continuous flow of organic material while ensuring optimal microbial activity through internal circulation of biogas and wastewater. This design allows for:
- Higher loading rates compared to conventional anaerobic digesters.
- Smaller reactor volume for the same treatment capacity.
- Efficient separation of biomass and effluent, leading to high-quality biogas production.
To fully leverage these advantages, automated process management plays a crucial role in monitoring and optimizing system performance in real-time.
The Benefits of Automated IC Process Management
1. Real-Time Process Monitoring and Control
Traditional anaerobic digestion operations rely on periodic manual sampling and analysis, which can lead to delays in detecting process fluctuations. Automation integrates advanced sensors and control systems to:
- Continuously monitor pH, temperature, biogas composition, and organic loading rates.
- Detect anomalies and automatically adjust parameters to maintain optimal conditions.
- Reduce reliance on human intervention, ensuring consistent system performance.
2. Optimized Biogas Production
An IC reactor’s efficiency depends on maintaining the right microbial balance. Automated control systems:
- Adjust feeding rates to prevent overload and underload scenarios.
- Regulate mixing and circulation to enhance biogas yield.
- Use predictive analytics to forecast gas production based on historical data and current process parameters.
By maximizing methane production, automated management improves the economic viability of anaerobic digestion operations.
3. Energy and Resource Efficiency
Automating IC process management reduces energy and resource consumption by:
- Optimizing pump and blower operations based on real-time demand.
- Reducing chemical dosing for pH control and nutrient balancing.
- Minimizing water and sludge disposal costs through precise waste stream management.
These efficiency gains lower operational costs and enhance sustainability.
4. Early Detection of Process Upsets
One of the greatest challenges in anaerobic digestion is process instability, which can result from toxic shocks, pH fluctuations, or temperature variations. Automated systems:
- Continuously track key performance indicators (KPIs).
- Issue early warnings and automatically adjust operational parameters.
- Prevent severe process disruptions, ensuring uninterrupted biogas production.
This proactive approach minimizes downtime and reduces maintenance costs.
Key Components of an Automated IC Process Management System
1. Smart Sensors and IoT Integration
Modern IC reactors are equipped with Internet of Things (IoT) sensors that provide real-time data on:
- pH levels to maintain an optimal microbial environment.
- Temperature for stable biological activity.
- Biogas flow rates to assess production efficiency.
- Organic load variations to adjust feeding strategies.
2. Automated Control Units
Programmable Logic Controllers (PLCs) and Distributed Control Systems (DCS) play a central role in managing IC reactors by:
- Processing sensor data and making automated adjustments.
- Controlling pumps, valves, and recirculation mechanisms.
- Reducing human error and optimizing operational efficiency.
3. Advanced Data Analytics and AI Optimization
Artificial Intelligence (AI) and Machine Learning (ML) improve IC process management by:
- Predicting performance trends and suggesting process improvements.
- Optimizing retention time and organic loading rates for enhanced biogas output.
- Detecting anomalies before they impact reactor stability.
4. Remote Monitoring and Cloud-Based Management
Operators can remotely access real-time data and control system settings via:
- Cloud-based dashboards accessible from anywhere.
- Mobile alerts and notifications for critical process deviations.
- Automated reporting for compliance and operational insights.
Applications of Automated IC Process Management
1. Industrial Wastewater Treatment
Food processing, breweries, and chemical industries use IC reactors to treat high-strength wastewater. Automation ensures:
- Compliance with environmental regulations.
- Efficient removal of organic contaminants.
- Enhanced energy recovery through biogas production.
2. Agricultural Biogas Plants
Farms generate large amounts of organic waste, which can be efficiently digested in IC reactors. Automated management:
- Improves digestion efficiency for manure and crop residues.
- Reduces labor-intensive monitoring.
- Ensures stable methane generation for on-site power use.
3. Municipal Wastewater Treatment
Municipalities facing increasing wastewater treatment demands benefit from automated IC reactors by:
- Reducing treatment plant footprint.
- Lowering energy consumption.
- Enhancing sludge stabilization and reuse potential.
Why Choose Center Enamel for Automated IC Process Management?
1. Cutting-Edge Technology
We integrate the latest automation and control solutions into our IC reactor systems, ensuring maximum efficiency and operational reliability.
2. Custom-Tailored Solutions
Every wastewater treatment facility has unique requirements. Center Enamel provides customized automation solutions tailored to specific operational needs.
3. Proven Industry Experience
With over 30 years of expertise, Center Enamel has successfully implemented high-efficiency anaerobic digestion systems in various industries worldwide.
4. Sustainable and Cost-Effective Solutions
Our automated IC process management systems:
- Reduce energy consumption and carbon footprint.
- Minimize operational and maintenance costs.
- Enhance long-term process stability and profitability.
Automated IC process management is transforming anaerobic digestion operations, delivering higher efficiency, increased biogas production, and enhanced process stability. By integrating real-time monitoring, AI-driven optimization, and remote access, Center Enamel’s advanced IC reactors provide a sustainable and cost-effective solution for wastewater treatment and biogas recovery.
For more information on how Center Enamel can optimize your anaerobic digestion operations, contact us today.